Order Picking: Your Guide to Efficient Inventory Management
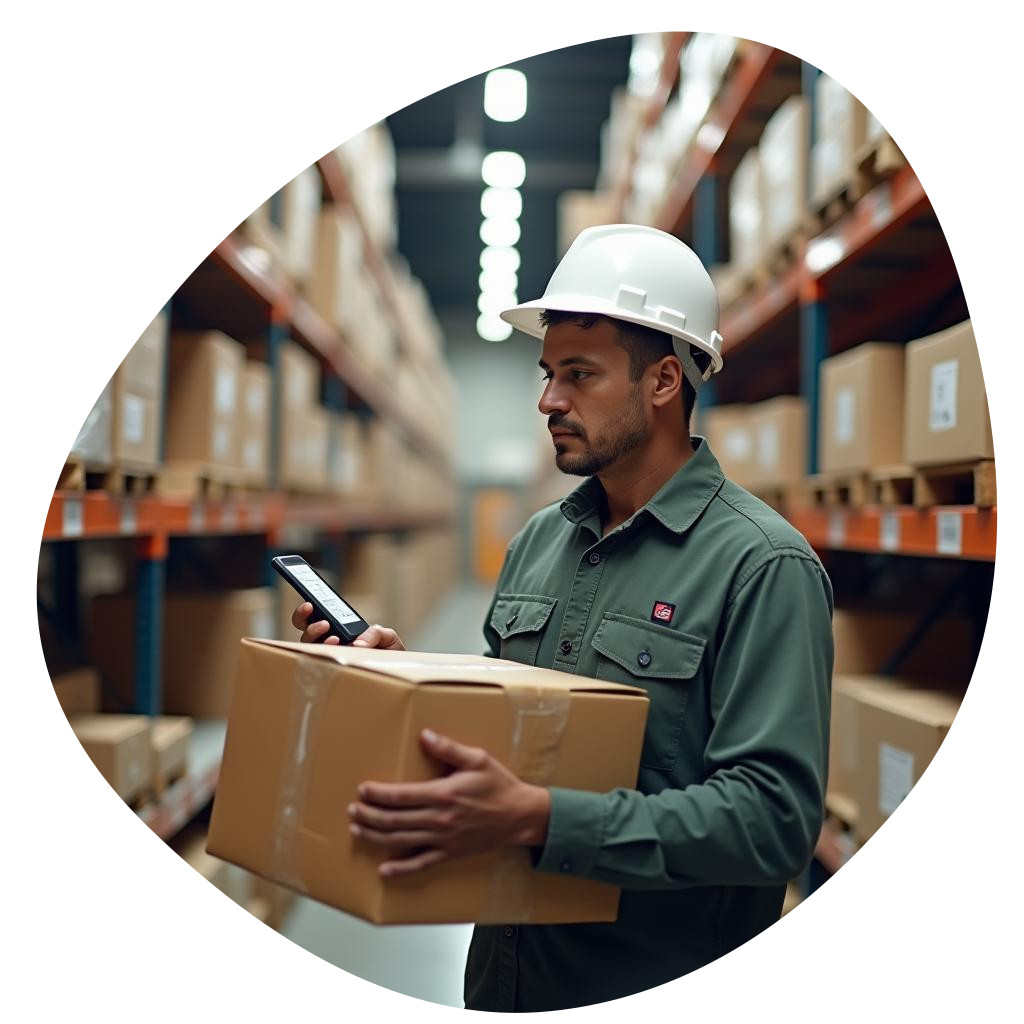
Introduction
Order picking stands as a cornerstone of warehouse operations, determining the efficiency and success of small to medium-sized ecommerce and retail businesses. At its core, order picking involves selecting the right products in precise quantities from storage locations to fulfill customer orders accurately and promptly.
In today's fast-paced business environment, the difference between thriving and struggling often comes down to how effectively a company manages its order fulfillment process. A well-designed picking system reduces errors, speeds up order processing, and ultimately leads to happier customers who receive exactly what they ordered, when they expected it.
The integration of a barcode inventory system transforms traditional picking operations into streamlined, digital workflows. By scanning products during the picking process, warehouse staff can verify selections instantly, maintain accurate inventory counts, and dramatically reduce picking errors. This technology provides real-time visibility into stock levels and picking progress, enabling managers to make informed decisions about resource allocation and process improvements.
Modern warehouse order picking encompasses various methods and technologies, each suited to different business needs and warehouse configurations. The choice of picking strategy significantly impacts operational efficiency, from basic paper-based systems to sophisticated cart-picking approaches. Successful businesses typically employ multiple order picking methods tailored to their specific product mix and order patterns.
Understanding these fundamental concepts helps build a foundation for optimizing warehouse operations. For businesses seeking comprehensive solutions, platforms like Finale Inventory offer flexible workflows that adapt to existing processes while introducing barcode scanning capabilities to enhance accuracy and speed.
Those interested in diving deeper into barcode-based solutions can explore our comprehensive guide to implementing a barcode inventory system, which details how this technology transforms inventory management across all warehouse operations.
Understanding Order Picking
Efficient order picking forms the backbone of successful warehouse operations, serving as the critical bridge between inventory storage and customer satisfaction. At its core, warehouse order picking involves staff members systematically retrieving specific products from their storage locations to fulfill customer orders accurately and promptly.
The Foundation of Order Picking
Order picking represents more than just grabbing items off shelves. It's a structured process that directly impacts shipping speed, accuracy rates, and ultimately, customer satisfaction. For smaller operations watching their bottom line, mastering this process can mean the difference between struggling with overhead costs and running a lean, profitable operation.
The Flow of Order Picking
When a customer places an order, the information flows from the ecommerce platform into the warehouse management system. Pickers receive detailed instructions about what items to retrieve and where to find them. Success hinges on three critical elements:
- Clear storage organization with logical product placement
- Accurate labeling of both products and storage locations
- Real-time inventory data that matches physical stock levels
Technology and Systems
Modern order picking systems enhance efficiency through guided workflows and real-time tracking. These systems range from basic digital pick lists to sophisticated solutions that optimize picking routes and track productivity metrics. Integration with barcode inventory management solutions proves particularly valuable, enabling quick product identification and location verification through simple barcode scans.
Small and medium-sized ecommerce businesses often see dramatic improvements in efficiency when implementing structured picking processes. With limited staff handling multiple responsibilities, a well-organized picking system reduces errors, speeds up order processing, and allows workers to handle higher order volumes without becoming overwhelmed.
Key Order Picking Methods
Selecting the right method for order picking directly impacts operational efficiency, labor costs, and accuracy rates. Understanding these order picking methods helps businesses make informed decisions about their warehouse operations.
Discrete or Basic Picking
Discrete picking involves completing one order at a time from start to finish. This straightforward approach works well for operations with smaller order volumes or when handling complex orders that require special attention. While it's the simplest method to implement, discrete picking integrates smoothly with pick and pack workflows, making it ideal for businesses just starting to formalize their fulfillment processes.
Batch or Multi Order Picking
Multi order picking combines several orders containing similar items into a single picking round. Instead of visiting the same storage location multiple times for different orders, pickers collect all needed items in one trip. For example, if three customers order the same type of shirt, a picker collects all three at once rather than making separate trips. This method particularly shines during holiday rushes or promotional periods when order volume spikes.
Zone Picking
Zone picking divides the warehouse into distinct sections, with dedicated pickers assigned to specific zones. This approach resembles a production line where orders move from zone to zone until completion. Zone picking excels when different storage areas require specific handling knowledge or when products vary significantly in size or picking complexity.
Wave Picking
Wave picking groups orders by specific criteria such as shipping deadlines or carrier routes. Orders might be picked in "waves" throughout the day – morning orders shipping same-day first, followed by next-day shipments in the afternoon. This structured approach helps maintain clear priorities and manage workflow peaks effectively.
The optimal approach often depends on your specific business needs. Many growing operations find success by combining methods – perhaps using zone picking for fast-moving items while maintaining discrete picking for special orders. As operations scale, specialized order picking systems and tools like a warehouse barcode scanner become invaluable for maintaining accuracy and speed across any chosen method.
Barcodes and Their Role in Speeding Up the Picking Process
Transitioning from traditional picking methods to barcode-enabled processes marks a significant leap in warehouse efficiency. Modern order picking systems rely heavily on barcode technology to maintain accuracy while increasing speed.
Streamlining with barcode scanning
Barcode scanning transforms picking accuracy by providing instant validation at each step. When workers scan items, the system immediately confirms whether they've selected the correct product, quantity, and location. This real-time verification dramatically reduces costly picking errors that can lead to customer dissatisfaction and returns.
Tools and setup
A reliable barcode scanner for inventory serves as the cornerstone of efficient picking operations. The scanner must be durable enough to withstand warehouse conditions while providing quick, accurate reads. Clear, standardized labeling proves equally crucial – proper barcode printing ensures consistent readability across your entire inventory.
Avoiding common pitfalls
Even well-implemented systems can face challenges. Environmental factors like poor lighting or damaged labels can slow down scanning. Workers may encounter misreads or connectivity issues that interrupt their workflow. For solutions to these challenges, consult our guide on common barcode problems and fixes. Addressing these issues early creates a solid foundation for implementing advanced order picking methods.
Why barcodes matter for growth
The benefits of a barcode inventory system extend far beyond basic scanning. Real-time inventory updates enable faster order fulfillment and better stock management. When integrated with picking operations, barcodes create a data-driven environment where managers can track productivity, identify bottlenecks, and make informed decisions about resource allocation. This visibility proves invaluable as businesses scale their operations and need to maintain efficiency while handling increased order volumes.
Essential Performance Metrics in Order Picking
Tracking the right metrics transforms warehouse operations from guesswork into a data-driven process that drives continuous improvement. Understanding and monitoring these key performance indicators helps businesses optimize their picking processes and maintain high service levels.
Primary Metrics That Matter
Pick Rate serves as a fundamental measure of warehouse productivity, typically expressed as lines picked per hour. This metric reveals how efficiently workers locate and retrieve items from storage locations. A warehouse might target 80-100 picks per hour for basic operations, though rates vary based on picking methods and layout.
Accuracy stands as equally crucial – even a 99% accuracy rate means one mistake per hundred picks, potentially leading to customer dissatisfaction and costly returns. Implementing proper warehouse order picking procedures, combined with barcode verification, helps maintain accuracy above 99.9%.
Secondary Performance Indicators
Travel time often consumes up to 60% of a picker's shift. Measuring average distance traveled per order helps identify opportunities to reorganize storage locations or implement more efficient picking strategies like batch picking.
Cycle time measurement tracks the entire order fulfillment process, from receiving the order to shipping. Fast cycle times directly impact customer satisfaction and inventory turnover rates.
Technology-Driven Improvement
Modern warehouses rely on shipping barcode scanner systems to automatically capture performance data while validating picks. This real-time data collection enables managers to spot trends and address inefficiencies promptly.
Multi order picking success depends heavily on measuring these metrics to fine-tune processes. For example, tracking pick rates across different zones helps optimize batch sizes and picker assignments. Regular analysis of these metrics, combined with proper tools and training, creates a foundation for sustainable operational excellence.
Examples of Order Picking Systems in Action
Strong order picking systems adapt to varying business needs while maintaining efficiency and accuracy. Consider how different approaches work in real-world scenarios:
Managing Peak Season Demands
A warehouse faces triple its normal order volume during holiday seasons. The order picking system automatically adjusts by:
- Reorganizing picking zones to minimize congestion
- Batching similar orders to reduce travel time
- Prioritizing orders based on shipping deadlines
- Balancing workload across available staff
Smart Automation Choices
While automated order picking systems offer impressive capabilities, businesses should focus on foundational improvements first:
- Start with barcode scanning and digital picking lists
- Add mobile devices for real-time updates
- Implement basic conveyor systems where practical
- Consider robotic solutions only after optimizing manual processes
Strategic Picking Methods
Successful warehouses often blend multiple picking strategies throughout the day:
The morning shift might employ multi order picking to handle bulk orders efficiently:
- Pickers collect items for multiple orders simultaneously
- Items are sorted into individual orders at packing stations
- This approach maximizes productivity during predictable volume periods
Afternoon operations might switch to discrete picking:
- Handles rush orders with greater precision
- Manages special handling requirements
- Processes high-value items requiring extra verification
A barcode inventory system ties these varied approaches together, ensuring accuracy from picking through shipping. For businesses ready to implement these improvements, detailed guidance is available in our guide on how to set up a barcode inventory system.
Wave picking schedules complement these methods by aligning with carrier pickup times, creating natural workflow cycles that keep orders moving smoothly through the facility.
Finale Inventory: Tailoring an Efficient Order Picking Solution
Finale Inventory stands apart in the warehouse management landscape by focusing on businesses that manage their own warehouse order picking processes. Rather than trying to be everything to everyone, Finale zeroes in on the sweet spot of organizations with 2 to 50 warehouse staff members, where efficiency and accuracy matter most but complex enterprise solutions would be overkill.
Real-Time Verification: Eliminating Common Warehouse Headaches
The cornerstone of Finale's approach is real-time verification through mobile barcode scanning. Every pick gets instant validation against the order, preventing costly mistakes before they happen. This systematic approach particularly shines when training seasonal workers or new staff members, as the scanner literally guides them to the correct bin location.
We use Finale to control inventory across 10 different sales channels, each with different selling profiles. We have individual products sold separately on one site which are sold together as a kit on another… Finale does everything we need it to and does it extremely well. – Ben Harper, Manager @ The USA Trailer Store
Flexible Picking Workflows That Scale
Finale Inventory adapts to various picking methods based on business needs:
- Wave picking for grouping similar orders
- Batch picking during high-volume periods
- Discrete picking for complex or specialized orders
The system's flexibility allows warehouse operations to evolve as order volumes grow without requiring a complete workflow overhaul.
Finale Inventory has really allowed us to effectively manage our warehouse… the real part that separates Finale from other WMS systems are the handheld scanners. No other system in this price range offers this functionality and it is a great time saver. – Reid Campbell, Owner @ Parts Haven
Smart Route Optimization
The software creates digital warehouse maps that optimize picking routes. This feature:
- Minimizes walking time between picks
- Updates stock levels instantly after each scan
- Prevents pickers from wandering the warehouse searching for items
Real-Time Decision Support
Warehouse staff can make informed decisions on the spot when challenges arise:
- Handle stockouts by reallocating inventory
- Split cases to fulfill partial orders
- Prioritize urgent shipments
- Check stock levels instantly
Integration and Scalability
Small and medium businesses appreciate Finale's ability to integrate with existing systems while maintaining simplicity. The platform connects seamlessly with various ecommerce platforms and shipping tools, creating a comprehensive fulfillment ecosystem that grows alongside the business.
We work closely with Finale, who always goes above and beyond to work through any questions we have, even coming up with creative solutions when necessary. The support truly outshines the software! – Richard B., Project Manager @ Warehousing
Practical Benefits for Growing Businesses
Finale Inventory's approach to order picking methods delivers tangible advantages:
- Reduced training time for new staff
- Fewer picking errors and returns
- Improved inventory accuracy
- Faster order fulfillment
- Lower operational costs
For businesses ready to streamline their warehouse operations, Finale Inventory offers a practical path forward. The system's proven track record with small and medium-sized operations demonstrates its value in transforming picking efficiency while maintaining accuracy.
Visit the barcode inventory system page to explore how barcode technology can revolutionize your entire warehouse operation.
Conclusion
Efficient order picking stands as a cornerstone of successful warehouse operations, directly impacting customer satisfaction and business growth. Through thoughtful implementation of proven order picking methods, businesses can transform their fulfillment processes from potential bottlenecks into streamlined workflows that consistently meet customer expectations.
The integration of barcode technology with well-designed order picking systems creates a powerful foundation for accuracy and speed. Small and medium-sized businesses that embrace these technologies find themselves better equipped to handle growth, seasonal fluctuations, and increasing customer demands without sacrificing precision or adding substantial overhead costs.
Modern warehouses thrive when they combine strategic picking methods with real-time data verification. By implementing barcode scanning throughout the picking process, businesses reduce errors while simultaneously creating an environment where new employees can quickly achieve proficiency. This technological backbone supports both accuracy and workforce flexibility, essential elements for sustainable growth.
Finale Inventory brings these critical elements together in a unified platform, offering businesses the tools needed to optimize their warehouse order picking operations. The system's real-time verification capabilities and adaptable framework provide the foundation necessary for businesses to scale their operations confidently.
For those seeking to further enhance their warehouse operations, the comprehensive barcode inventory system guide offers additional insights into maximizing efficiency and accuracy throughout the fulfillment process.
Frequently Asked Questions
What is order picking and how does it work?
Order picking is the essential warehouse process of gathering specific products from inventory to fulfill customer orders. At its core, order picking involves warehouse staff systematically retrieving items from their storage locations, verifying correct quantities against order requirements, and preparing these items for shipment. Effective warehouse order picking depends heavily on proper organization, clear storage location labeling, and maintaining accurate real-time inventory data to ensure pickers can quickly locate and retrieve the right products.
What are the different methods of order picking?
The main order picking methods include discrete picking where one order is picked at a time, batch picking which combines multiple orders into a single picking trip, wave picking that organizes picks by time windows, and zone picking where workers are assigned to specific warehouse areas. Each of these order picking methods offers distinct advantages – discrete picking excels in accuracy for small operations, while batch picking significantly improves efficiency for higher volume operations. Most modern implementations incorporate barcode scanning technology to validate picks and maintain accuracy.
What is task consolidation in order picking?
Task consolidation combines multiple warehouse activities into unified workflows to maximize efficiency. For example, workers might pick items for several orders simultaneously while performing cycle counts along their picking route. This approach eliminates redundant warehouse trips and makes better use of worker time. Modern barcode-driven systems make this consolidation practical by providing real-time validation and clear task sequencing that keeps complex combined workflows organized and accurate.
How can order picking processes be optimized?
Optimizing order picking starts with fundamental elements like strategic warehouse layout design and implementing proper tools like barcode scanners, but the right picking method for your operation is equally crucial. Measuring key performance indicators such as picks per hour, travel time between picks, and accuracy rates helps identify process bottlenecks. Software solutions like Finale Inventory provide real-time visibility into these metrics while offering guided picking workflows that naturally lead workers through optimal pick paths.
What equipment is needed for efficient order picking?
Essential order picking equipment includes properly configured storage solutions like shelving and bins, ergonomic picking carts, and critically important warehouse barcode scanner devices for real-time inventory validation. The scanning technology acts as a crucial accuracy tool, instantly confirming correct item selection. Clear, standardized product labeling with scannable barcodes on both storage locations and products creates an environment where mistakes become much harder to make.
Why is accuracy so crucial in order picking?
Order picking accuracy directly impacts customer satisfaction and business reputation. When orders are picked incorrectly, it triggers a cascade of problems including customer returns, inventory discrepancies, and potential overselling of items thought to be in stock. Accurate picking also affects operational efficiency since errors require expensive correction processes. Implementing barcode validation at the point of picking creates a robust verification system that maintains consistently high accuracy rates.
Does order picking software integrate with shipping carriers?
Modern order picking platforms typically offer robust shipping carrier integration, allowing seamless transfer of order details from picking to shipping. These systems can automatically send picked order information to shipping barcode scanner systems, streamlining the final stages of order fulfillment. By eliminating manual data entry between picking and shipping systems, businesses reduce errors while accelerating the time from pick completion to carrier handoff.
Seamless Barcode Integration
Set up your inventory for long-term growth with barcoding automation